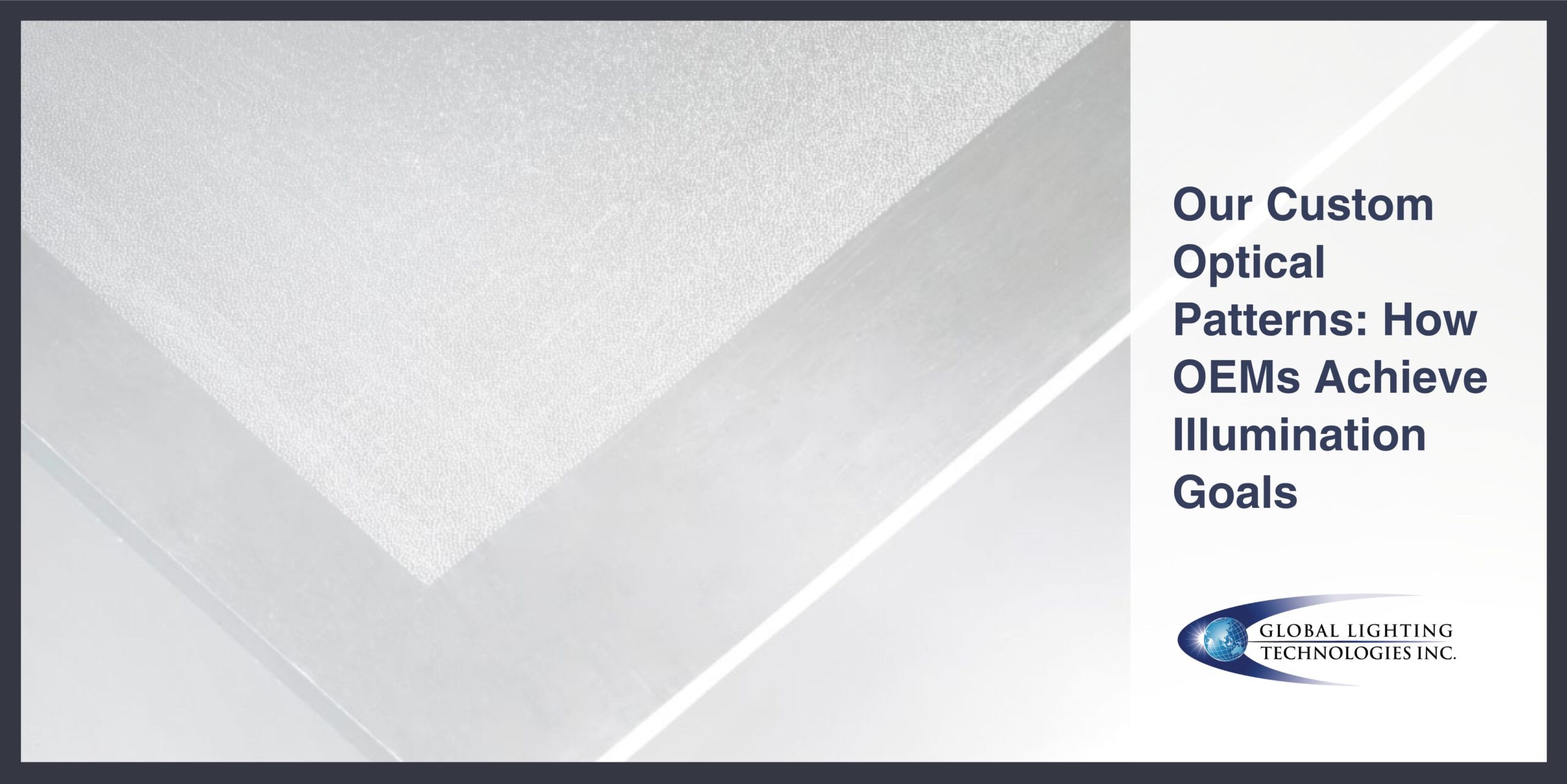
Custom Light Guide Design Maximizes Your Manufacturing Investment
You seek unparalleled performance and precision for your product or application. A custom optical pattern in your light guide design is the answer. For project leaders who’ve identified the need for a light guide, I can’t underscore enough how crucial it is to understand the impact of a custom optical pattern with microstructures. I spoke with Global Lighting Technologies Sales Project Manager Jonathan Tarnay, who breaks down important concepts that bring clarity to the importance of this technology.
Read on for his explanation of what optical patterns are and to delve deeper into how they create uniform, impactful light guides.
What Are Optical Patterns?
Before you learn about optical patterns, it’s helpful to have a background on what light guides are, what they achieve and how. I often share this helpful primer, What is a Light Guide?, with OEM decision makers; it covers light guide component basics like optical patterns.
Now, we can dive into optical patterns specifically. An optical pattern is a series of microstructures embossed or molded within a light guide which interrupt total internal reflection to extract light and achieve a uniform light output. If that sounds complex, here’s another way to think about optical patterns: “They’re very small, strategically placed structures on a light guide plate that redirect light,” says Jonathan.
Microstructures include prisms, lenses or other features that shape the light and create specific lighting patterns or effects. Optical patterns control the direction, intensity and distribution of light.
“Without an optical pattern, light remains inside the light guide because it’s below the critical angle of the light path. This is total internal reflection, which needs to be interrupted for light to leave the light guide. Micro-structures, or optical patterns, change the angle at which light strikes the surface. This alters its path and directs the light out.”
Below, you can see how light from the light source reflects inside the plate until it hits the optical pattern (micro-structure) which redirects it out of the structure.
Light Guide Plate Materials & Optical Pattern Application Methods
At Global Lighting Technologies, we typically craft light guide plates from acrylic and polycarbonate. The performance is similar, but there are several notable differences:
- Polycarbonate is 88% transmissible. It can be thinner than acrylic and is shatter-resistant. It’s often used in automotive applications because, in some specifications, it meets flammability ratings that acrylic does not.
- Acrylic is 92% transmissible, so compared to polycarbonate, it allows for a slightly brighter light guide. Additionally, it can be used in more applications than polycarbonate.
Our optical patterns are applied to light guide plates in two different ways: injection molding or embossing. Jonathan comments, “Injection molding allows for more complex geometry and microstructure features. Light guide plate material is injected into a mold containing the optical pattern. For extrusion and thin film embossing, the optical pattern is etched into a metal cylinder then rolled onto the light guide plate material.”
Learn more about how our thin, flexible technology meets the future of lighting.
Our Light Guide Design Process
“We decide on optical patterns and microstructures early on in our design process. We closely collaborate with customers to achieve the optical performance the customer is looking for,” says Jonathan. Consequently, this is why we recommend customers bring our team into a project as early as possible.
During the design process for every project, we dig into a customer’s requirements and goals before customizing their optical pattern. First, we determine how the project is illuminated. The number of LEDs, their locations and their brightness requirements guide us on how to design and place our optics. Because our engineers work from an established set of optical patterns and guidelines, they have the experience to recommend the right pattern fit for each project.
Next, we decide how to create the optical pattern and microstructures. Jonathan describes the evolution of this process: “As we’ve evolved, we’ve begun to employ laser microstructures and micro-machined structures. Micro-machined structures are unique to Global Lighting Technologies application. These mirror-finished structures allow us to control a light path’s direction. This is a game-changer for customers who require very specific light distributions!”
The microstructures that make up the optical pattern are determined by the tool that creates them, whether laser or micro-machining. When determining the density and locations of the pattern, we use software to create a map of all the pattern locations. Then, they’re converted to machine code that the laser or micro-machining equipment uses to physically create the pattern and microstructures.
Optical Pattern, Microstructure and Light Guide Testing
Before production, we test our light guide design with simulation software. This pinpoints design innovations without expending the costs for tooling, which presents added value to our customers. It reduces the time and increases confidence that the pattern design is effective.
Jonathan says that after simulation testing is complete, “we prototype our light guides to conduct physical tests. Based on our testing, we know that light guides are very resilient. Our light guides are components of products used in the arctic, desert and jungle!”
The pattern durability in different temperatures and humidity levels is determined by the light guide plate material. This is why our reliability testing equipment is crucial. The equipment submits our light guides to extreme temperatures and humidity to ensure that they perform well in all reasonable environments.
We also validate optical patterns with laser microscopes to observe and measure the pattern profile to confirm if it achieves the customer’s performance targets.
U.S. Team, Global Capabilities for Optical Pattern Design
I’m always proud to share that our team customizes optical patterns that are actually feasible because we manufacture what we design. Unlike firms that only provide optical pattern design and don’t have production in mind, we consider the whole process from the start.
We have specialized optical teams that focus on studying our optical patterns and light guide designs. Equally important, all our engineers understand optical pattern development and work with customers to determine the best fit. Our U.S. engineers are hands-on through the entire project from beginning to end. Even as light guides go into production in one of our five global facilities, there is consistent communication from the U.S. team to customers.
Light guides, including optical pattern and microstructure design, can seem complex. Our team is ready to smooth your path to production and guide you through each step! Connect with my team here to share your bright idea!