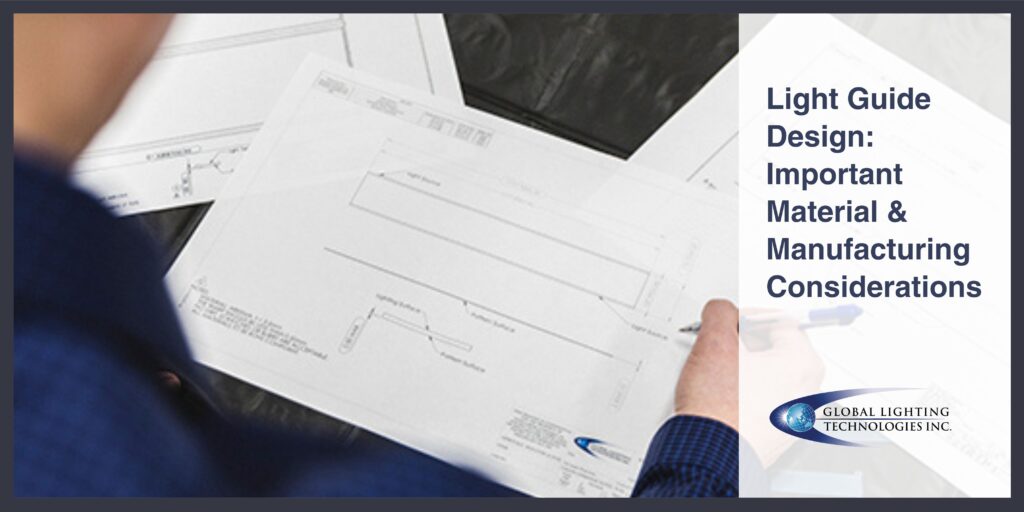
Why Component Selection Matters in Light Guide Design
During light guide design, I find our customers often focus on cost and general performance but overlook how critical each component is to long-term efficiency, durability, and product success. I’ve seen how material and optical pattern choices can create efficient products that meet benchmarks. Conversely, poorly chosen materials can lead to uneven brightness, wasted energy, or costly redesigns. Understanding how each part of a light guide affects its function is essential to achieving optimal illumination, cost efficiency, and manufacturing feasibility.
A strong light guide design ensures even light distribution, minimizes power consumption, and enhances the overall product experience. Below, I explore key design considerations, from optical patterns and LED pairing to material selection and manufacturing techniques, to help you make strong light guide design choices. If you’re unfamiliar with basic light guide components, I suggest starting with our Light Guide Primer for helpful context!
Component: Optical Patterns – Precision Control for Maximum Illumination Efficiency
Optical patterns are microstructures on the surface of a light guide that extract and direct light to ensure uniform distribution. Without them, light would remain trapped within the guide, leading to poor illumination and inefficiencies.
Solving Common Illumination Challenges
One of the primary advantages of custom optical patterns is their ability to eliminate hotspots and uneven lighting. These patterns create a smooth, uniform output by controlling how light exits the viewing area. They also play a crucial role in blending light from multiple LEDs, preventing color shifts and inconsistencies.
Custom patterns also reduce power consumption by improving light extraction efficiency. When light is more effectively directed, engineers can use fewer LEDs while maintaining the same brightness, ultimately lowering costs and energy use.
Real-World Impact: Optimizing LED Efficiency
A common challenge for OEMs is managing direct-lit designs, where LEDs produce harsh hotspots. We often work with customers who initially design products with excessive LEDs to compensate for poor uniformity. By applying a tailored optical pattern, we can reduce the number of LEDs needed, improving efficiency while maintaining high-quality illumination. This is especially valuable in industries such as consumer electronics, where compact designs demand precise light control.
Component: Light Sources – Achieve the Right Balance
Choosing the right LED type and placement is crucial to a light guide’s performance. Top-firing and side-firing LEDs are the most used, with placement affecting brightness, uniformity, and efficiency. Poorly positioned LEDs can lead to bright spots or dim areas, reducing overall effectiveness.
An additional design feature that enhances LED efficiency is a lens array at the coupling point between the LED and the light guide. This increases the distribution angle, covering more area with fewer LEDs, which improves efficiency and reduces power consumption.
Reduced LED Count Through Smart Optical Design
One of the biggest trade-offs in LED pairing is the balance between LED count and optical design. A well-optimized optical pattern allows engineers to space LEDs further apart while maintaining uniform brightness. For example, in exit signs, instead of placing LEDs on both edges of the light guide, we increase the density of the optical pattern near the farthest edge to pull light through more effectively. This approach lowers manufacturing costs and power consumption without sacrificing performance.
Industry-Specific Considerations
Different industries have varying LED requirements. Automotive applications, for example, require LEDs that meet the AEC-Q101 standard to ensure reliability under extreme conditions, while consumer electronics prioritize compact designs. Understanding these nuances is critical to selecting the best LED and light guide combination for a specific application. I’m proud that my team has the knowledge and experience to help our customers make informed choices.
Component: Materials – Balance Light Transmission, Durability, and Cost
Two of the most commonly used materials for light guides are acrylic and polycarbonate. Acrylic provides excellent optical clarity and is the preferred choice for most applications due to its high light transmission efficiency. Polycarbonate, on the other hand, offers greater impact resistance but slightly lower optical performance.
How Material Choice Affects Performance
Material selection plays a critical role in brightness, color accuracy, and efficiency. A poorly chosen material can lead to excessive light loss, reducing the effectiveness of the light guide. For example, our team has tested multiple alternative materials to our primary acrylic source but has repeatedly found that they fail to meet optical and dimensional requirements. We continue to test dozens of materials to provide customers with a range of good options.
Sustainability and Emerging Material Innovations
Many industries increasingly prioritize sustainability. At Global Lighting Technologies, we actively research recycled resin materials to improve environmental impact without sacrificing performance. This shift is driven by consumer demand for sustainable product design.
Now that we’ve covered the main light guide components, let’s explore our proven manufacturing processes.
Consideration: Manufacturing Processes & Their Impact on Performance
Light guides can be produced using various techniques, including:
- Injection Molding – Ideal for complex shapes and high-volume production.
- Extrusion Embossing – Suitable for producing thin, flexible light guides with continuous lengths.
- Thin-Film Embossing – A cost-effective solution for lightweight, high-efficiency optical surfaces.
Manufacturing Challenges and Cost Trade-offs
The complexity of a light guide’s geometry significantly impacts manufacturing feasibility and cost. More intricate designs require precision tooling and can lead to higher production expenses. Dual-shot molding, which combines the housing and light guide in a single tool, can reduce costs but requires an upfront investment in tooling.
For OEMs looking to integrate light guides into their products, I recommend prioritizing power requirements and spatial constraints from the start. Prior to manufacturing, it’s crucial to ensure sufficient room for proper light transition and optical patterns. This prevents costly redesigns and inefficiencies.
OEM Involvement in Manufacturing Decisions
While our engineers recommend the optimal manufacturing process, our customers play a role in final decisions based on cost and scalability. We often provide multiple quotations to keep our customers informed.
Optimizing Light Guide Performance for Any Application
Selecting the right materials, optical patterns, LED configurations, and manufacturing techniques is essential for achieving efficient and cost-effective light guides. Uninformed choices can lead to performance inefficiencies, while well-informed decisions result in superior illumination, lower power consumption, and long-term cost savings.
By working closely with a knowledgeable design team, companies can achieve high-performance, energy-efficient lighting solutions tailored to their specific application needs. Contact our team today to get started!